The vertical mixer is an essential component for anyone working with plastics materials, but also with grains, cereals, rubber crumbs and more.
Choosing the right model can make all the difference in terms of efficiency and mixing quality. But what needs to be evaluated before buying?
In this guide we look at all the key factors to help you choose a suitable industrial vertical mixer for your production needs.
Before asking for a quotation, please consider:
- Capacity required in lt. or m3 or kg..Vertical mixers are available in different standard capacities bu we can construct mixers bespoke to your project.
- It is important to verify not just the height in the premises, without forgetting the tolerance needed to stand it up, but also the entrance width and height,
- You must decide how to fill the mixer: from top through pneumatic system (in this case consider the cyclon), from top-side, from a big bag held on a slide on the loading hopper or through a driven horizontal screw.
- It is important to let us know what material, shape, bulk density the mixer will process.
- The machine can be driven by pulley and belts or by gearmotor.
- Discharging can be done through a side pipe which will directly fill a big bag.
- The side pipe can be connected to a single or double bag filling station, with or without load cells. With automated dual flow valve.
- A PLC can connect multiple buffers, mixers, bag filling stations and even plastic extruders or other machines in order to control a whole production system.
- Also the mixer can be positioned on load cells, always connected to a scale and possibly a label printer.
- On the lower part of the mixer you will find a discharging pipe with a valve which will allow you to quickly empty the machine. The material can fall into a hopper connected to an endless screw to lift the material up to a feeding point on the next machine.
- A hatch at the bottom of the vertical screw will be used for cleaning purposes.
- The mixer can be constructed in sturdy carbon steel, coated with anti-rust and paint or in AISI304 stainless steel, particularly suggested for materials which can have humidity residues, when the machine must be cleaned thoroughly between batches and when the machine must be kept outdoors.
- Level control is given by transparent PC windows along the barel and by minimum and/or maximum level indicators with sound and visual alarms. These will give the operators an immediate perception of the quantity of material inside the machine. The level controls can be connected to the PLC, when controlling a whole system, to interact with the other machines.
To increase the mixing capacity, you can consider a crossed mixing system, consisting of 2 or more high capacity mixers with communicating cross-pipes which will convey material from one mixer to the other in order to still better mix different batches.
At Germanplast we have been designing and manufacturing custom-made vertical mixers for over 30 years, reliable, efficient and designed to last, with a focus on efficiency and after-sales support.
Contact us for a free consultation or a customised quote! Visit our selection of vertical mixer and our youtube channel!
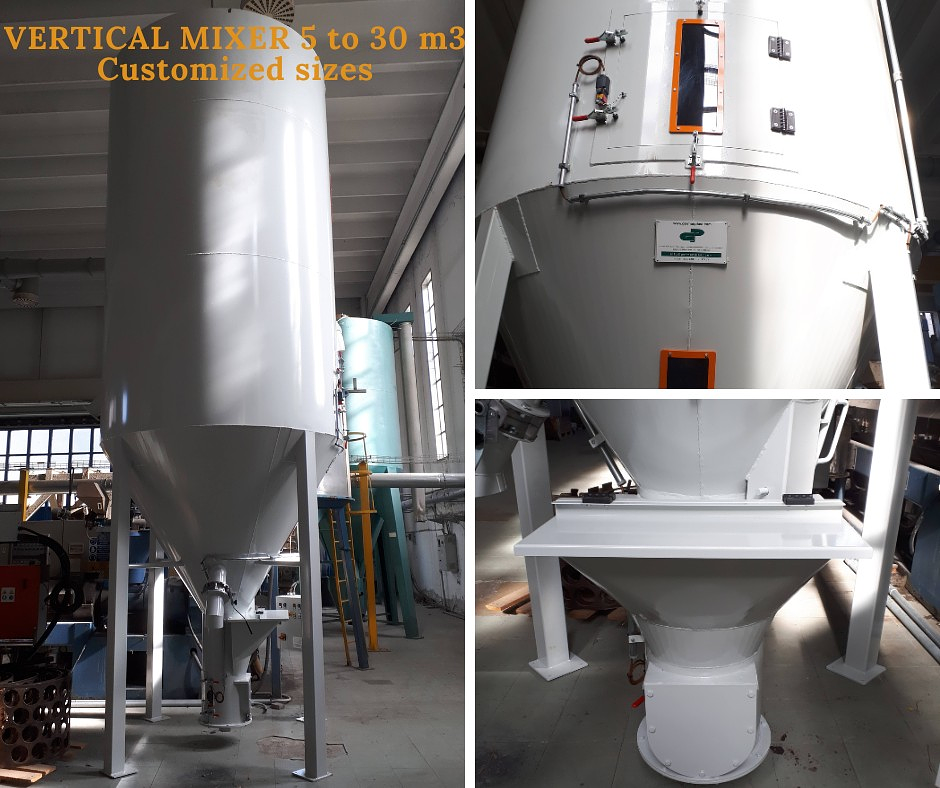